Value Engineering vs.
Vergleich zwischen Value Engineering und Lean Management
Value Engineering und Lean Management sind zwei Ansätze, die Unternehmen dabei helfen, ihre Prozesse zu optimieren und ihre Effizienz zu steigern sowie Kosten zu senken. Obwohl sie sich in einigen Aspekten ähneln, gibt es auch signifikante Unterschiede zwischen den beiden.
Gemeinsamkeiten
Lean Management und Value Engineering haben das gemeinsame Ziel, Effizienz zu steigern und Verschwendung zu reduzieren, indem sie Prozesse und Produkte optimieren. Beide Methoden zielen darauf ab, Mehrwert zu schaffen, allerdings unterscheiden sie sich in ihrem Fokus:
Lean Management konzentriert sich auf die Optimierung von Prozessen durch die Beseitigung von nicht-wertschöpfenden Aktivitäten in der gesamten Wertschöpfungskette. Es reduziert Verschwendung und verbessert die Effizienz in der Produktion und Verwaltung.
Value Engineering hingegen fokussiert sich auf das Produktdesign und die Materialkosten, indem es alternative Möglichkeiten untersucht, um die notwendigen Funktionen eines Produkts zu einem geringeren Gesamtkostenaufwand zu realisieren.
Gemeinsam fördern beide Methoden die Kostenreduktion, die Kundenzufriedenheit und die Qualitätssteigerung durch systematische Ansätze zur Prozess- und Produktverbesserung.
Zielbereiche
Lean Management wird in der Regel auf betriebliche Prozesse angewendet, um die Effizienz in der Produktion, Logistik oder Verwaltung zu steigern. Es zielt auf die Verbesserung von Arbeitsabläufen und die Vermeidung von unnötigen Schritten oder Fehlern.
Value Engineering wird auf Produkte oder Projekte angewendet, um deren Funktionen zu optimieren und dabei die Herstellungskosten zu reduzieren. Es geht um die Suche nach Einsparungspotenzialen im Design und in den Materialkosten.
Methode
Lean Management setzt auf Werkzeuge wie Kaizen, 5S, Kanban und Just-in-Time, um Prozesse kontinuierlich zu verbessern und Verschwendung zu beseitigen.
Value Engineering nutzt Ansätze wie Funktionsanalyse,
Kostenermittlung und alternative Materialsuche, um den Wert eines Produkts zu maximieren und die Kosten für dessen Herstellung zu minimieren.
Auswirkungen
Lean Management beeinflusst vor allem die Effizienz und Produktivität der internen Abläufe und kann kurzfristig zu verbesserten Durchlaufzeiten und Kostenreduktion führen.
Value Engineering hat direkten Einfluss auf die Produktkosten und das Design, was langfristig zu nachhaltigen Kostensenkungen bei der Materialbeschaffung und Herstellung führt.
Welche Methode eignet sich besser für Kostenreduktion?
Value Engineering erzielt tendenziell höhere Einsparungen, da es direkt die Materialkosten und das Produktdesign optimiert, die oft den größten Teil der Gesamtkosten ausmachen.
Die Werkzeuge von Lean Management
Lean Management bietet eine Vielzahl von Werkzeugen, die Unternehmen dabei unterstützen, Prozesse effizienter zu gestalten, Verschwendung zu minimieren und kontinuierliche Verbesserungen in der gesamten Wertschöpfungskette zu fördern.
KAIZEN
Kaizen ist ein zentraler Bestandteil von Lean Management und bedeutet auf Japanisch „kontinuierliche Verbesserung“. Es beschreibt einen fortlaufenden Prozess, der darauf abzielt, durch kleine, inkrementelle Veränderungen Arbeitsprozesse effizienter zu gestalten und Verschwendung zu reduzieren.
Kaizen fördert die aktive Einbindung aller Mitarbeitenden, um Abläufe, Qualität und Produktivität kontinuierlich zu optimieren. Der Ansatz konzentriert sich darauf, bestehende Prozesse in kleinen Schritten zu verbessern, anstatt auf radikale Umgestaltungen zu setzen.
Kaizen zielt auf eine langfristige, nachhaltige Steigerung der Wettbewerbsfähigkeit eines Unternehmens.
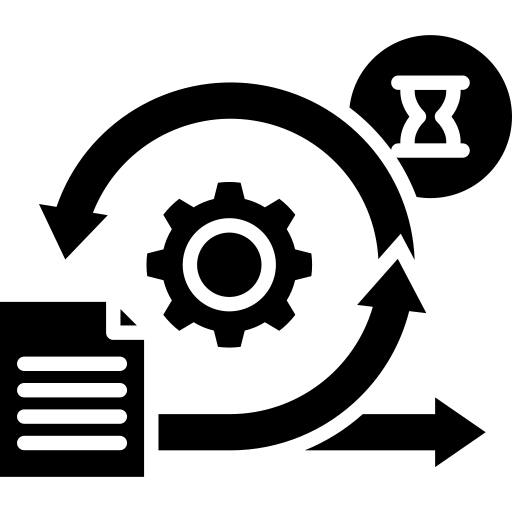
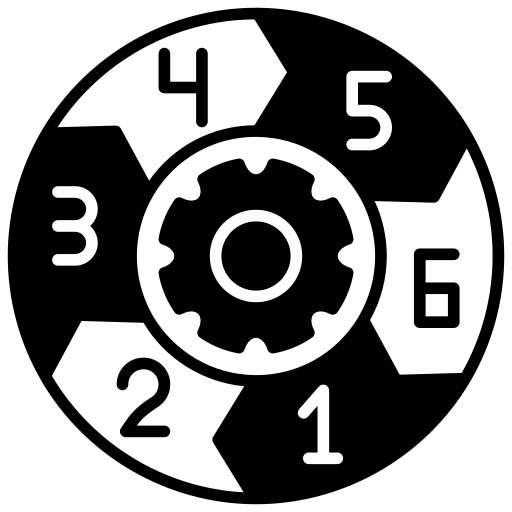
6 – S
6S im Lean Management ist eine erweiterte Methode des 5S-Systems, das darauf abzielt, Arbeitsplätze zu organisieren, die Effizienz zu steigern und Verschwendung zu reduzieren. Die 6S-Methode fügt dem klassischen 5S-System (Sortieren, Setzen, Säubern, Standardisieren, Selbstdisziplin) ein sechstes Element hinzu: Sicherheit.
Die sechs Schritte der 6S-Methode sind:
Sortieren (Sort): Trennen von notwendigen und unnötigen Materialien, um den Arbeitsplatz zu optimieren.
Setzen (Set in Order): Anordnung von Arbeitsmitteln und Werkzeugen für maximale Effizienz und Zugänglichkeit.
Säubern (Shine): Regelmäßige Reinigung des Arbeitsplatzes zur Vermeidung von Verschmutzungen und Unfällen.
Standardisieren (Standardize): Schaffung einheitlicher Verfahren und Standards zur Aufrechterhaltung eines organisierten Arbeitsplatzes.
Selbstdisziplin (Sustain): Förderung einer Kultur, in der die Einhaltung der 6S-Prinzipien zur Gewohnheit wird.
Sicherheit (Safety): Integration von Sicherheitsmaßnahmen, um Arbeitsunfälle zu vermeiden und die Gesundheit der Mitarbeiter zu schützen.
Durch die Einführung von Sicherheit als sechstes Element zielt 6S nicht nur auf die Verbesserung der Effizienz und Organisation, sondern auch auf die Schaffung eines sicheren und gesunden Arbeitsumfelds ab.
KANBAN
Kanban ist ein zentrales Werkzeug im Lean Management, das zur Visualisierung und Steuerung von Arbeitsprozessen dient. Ursprünglich in der Automobilproduktion entwickelt, ermöglicht Kanban eine flexible und effiziente Steuerung des Materialflusses und der Produktion. Das System basiert auf der Nutzung von Karten oder Tafeln, die den Fortschritt von Aufgaben oder Materialbewegungen in einem kontinuierlichen Fluss anzeigen.
Ziel von Kanban ist es, Überproduktion und Verschwendung zu vermeiden, indem nur dann produziert wird, wenn eine tatsächliche Nachfrage besteht. Dies wird durch das Pull-Prinzip erreicht, bei dem nach Bedarf Material oder Arbeitspakete “gezogen” werden, anstatt sie in Erwartung zukünftiger Anforderungen zu “schieben”.
Im Bereich Lean Management fördert Kanban eine kontinuierliche Verbesserung und sorgt für Transparenz in Arbeitsprozessen, da Engpässe und Ineffizienzen schnell identifiziert und beseitigt werden können. Es ist besonders nützlich in Bereichen, die eine hohe Flexibilität erfordern, wie etwa der Produktion, der Softwareentwicklung oder dem Projektmanagement.
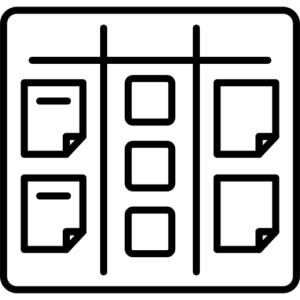
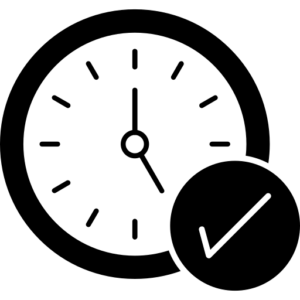
JUST-IN-TIME
Just-in-Time (JIT) ist ein zentrales Prinzip im Lean Management, das darauf abzielt, Material, Komponenten und Produkte exakt dann bereitzustellen, wenn sie im Produktionsprozess benötigt werden. Ziel ist es, Lagerbestände und damit verbundene Kosten auf ein Minimum zu reduzieren. Durch die Synchronisation von Produktion und Bedarf wird Verschwendung in Form von Überproduktion und unnötigen Lagerkosten vermieden. JIT erfordert eine präzise Abstimmung der Lieferketten, eine hohe Flexibilität der Lieferanten und eine effiziente Produktionsplanung, um sicherzustellen, dass Materialien in der richtigen Menge und zur richtigen Zeit verfügbar sind.